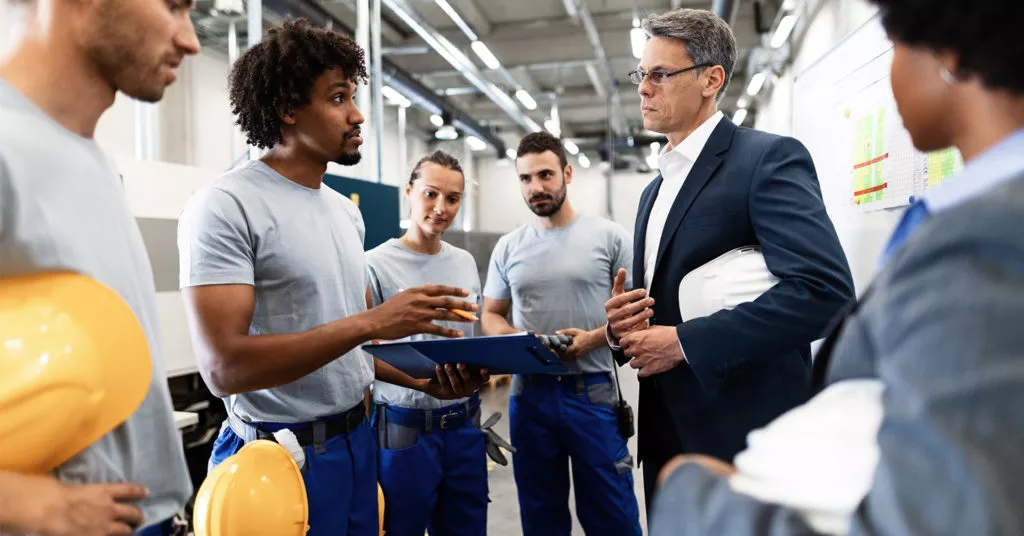
Building a Workplace Safety Culture in 8 Steps
A strong workplace safety culture is key to any successful safety program. In this article, learn how to build one of your own in 8 steps.
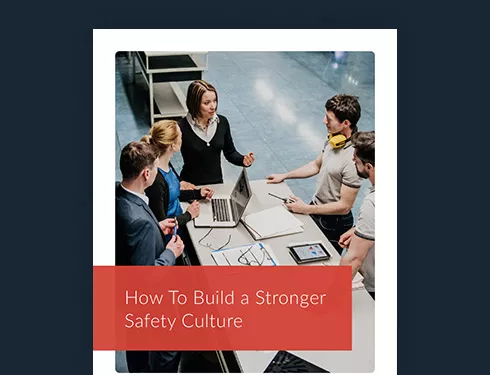
Workplace safety is quickly becoming one of the most important considerations for employees. Of the workers surveyed in the 2025 Employee Safety Report, 96% of U.S. and U.K. employees say their physical safety is important to them.
For employers, attracting committed employees is just one pain point calling for a safer workplace. The National Safety Council estimates that the total cost of workplace injuries and fatalities in 2020 was $163.9 billion. Beyond that, poor safety can cost an organization more in health benefits, turnover, and brand and reputation damage.
Safety issues indicate broader organizational misalignment. By building a safety culture within your company from the ground up, you will have the necessary foundation for effective safety policies, emergency plans, and company-wide engagement. Here, we’ll explore the steps involved in realigning your safety management and creating a strong safety culture.
Download Our How To Build a Stronger Safety Culture Guide
What Is Safety Culture in the Workplace?
Safety culture describes the collection of values, priorities, beliefs, mindsets, and ideals that inform behaviors and experiences related to safety.
Safety culture can refer to the organizational and individual “attitudes” toward safety. And it falls under the umbrella of the overall workplace culture. A company’s safety culture can be positive, negative, or somewhere in between, and it has a significant impact on safety outcomes.
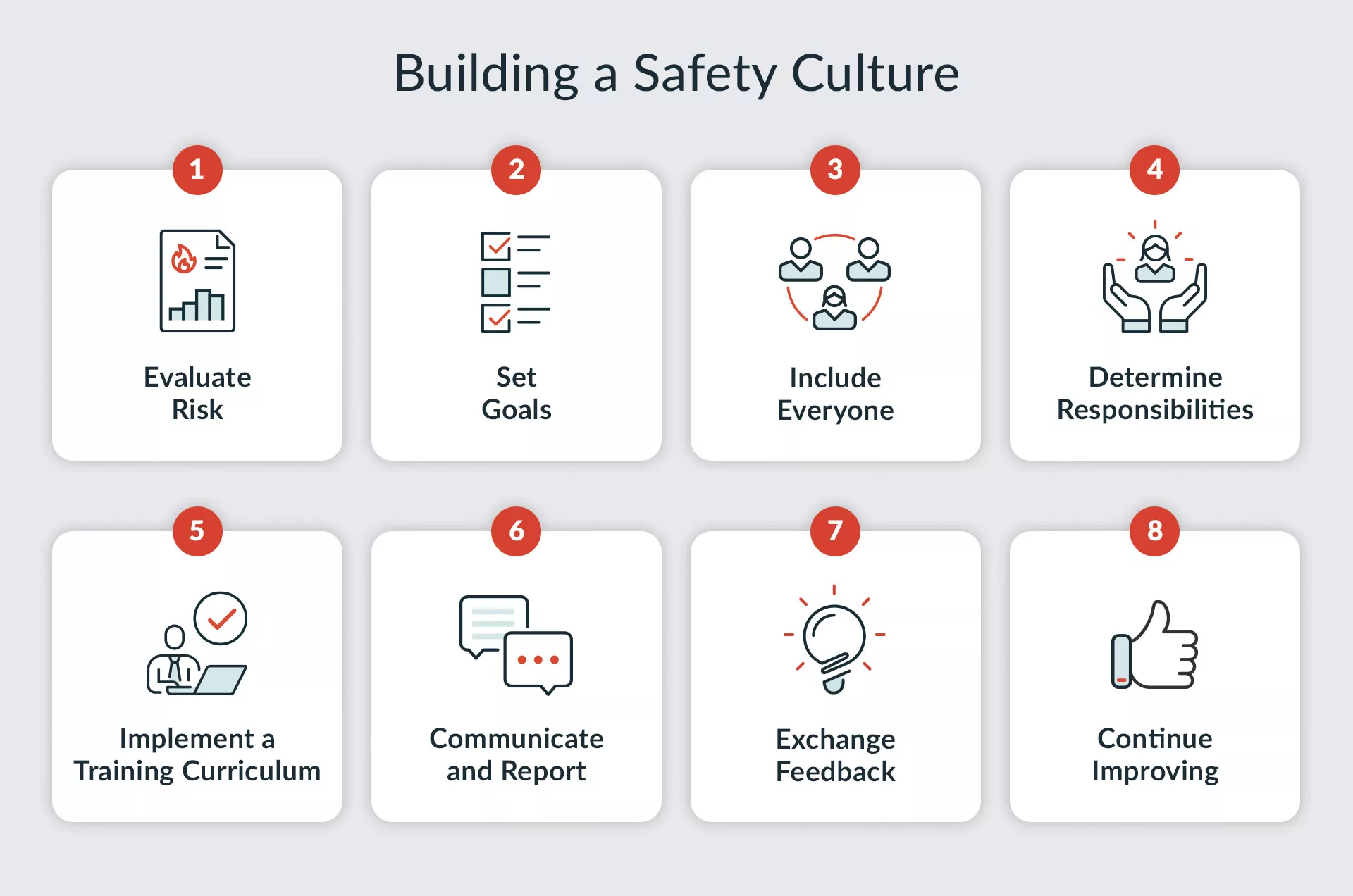
How To Build a Strong Safety Culture
Step 1: Evaluate risks and existing response plans
In order to build a safety culture that encourages proactive risk management, you’ll first need to get the lay of the land, the “threat landscape,” if you will.
Think through every part of your business. Consider what risks your people and operations face with a tool like a business threat assessment. Analyze the likely severity and frequency of any given threat, and prioritize preparedness efforts based on the overall risk. If your organization already has existing plans for any given situation, review them regularly to ensure they are as effective as possible at mitigating harm.
Once you have evaluated the kinds of threats your organization might face and have committed to countering them, it’s time to start setting goals and developing successful safety procedures for the entire organization to adopt.
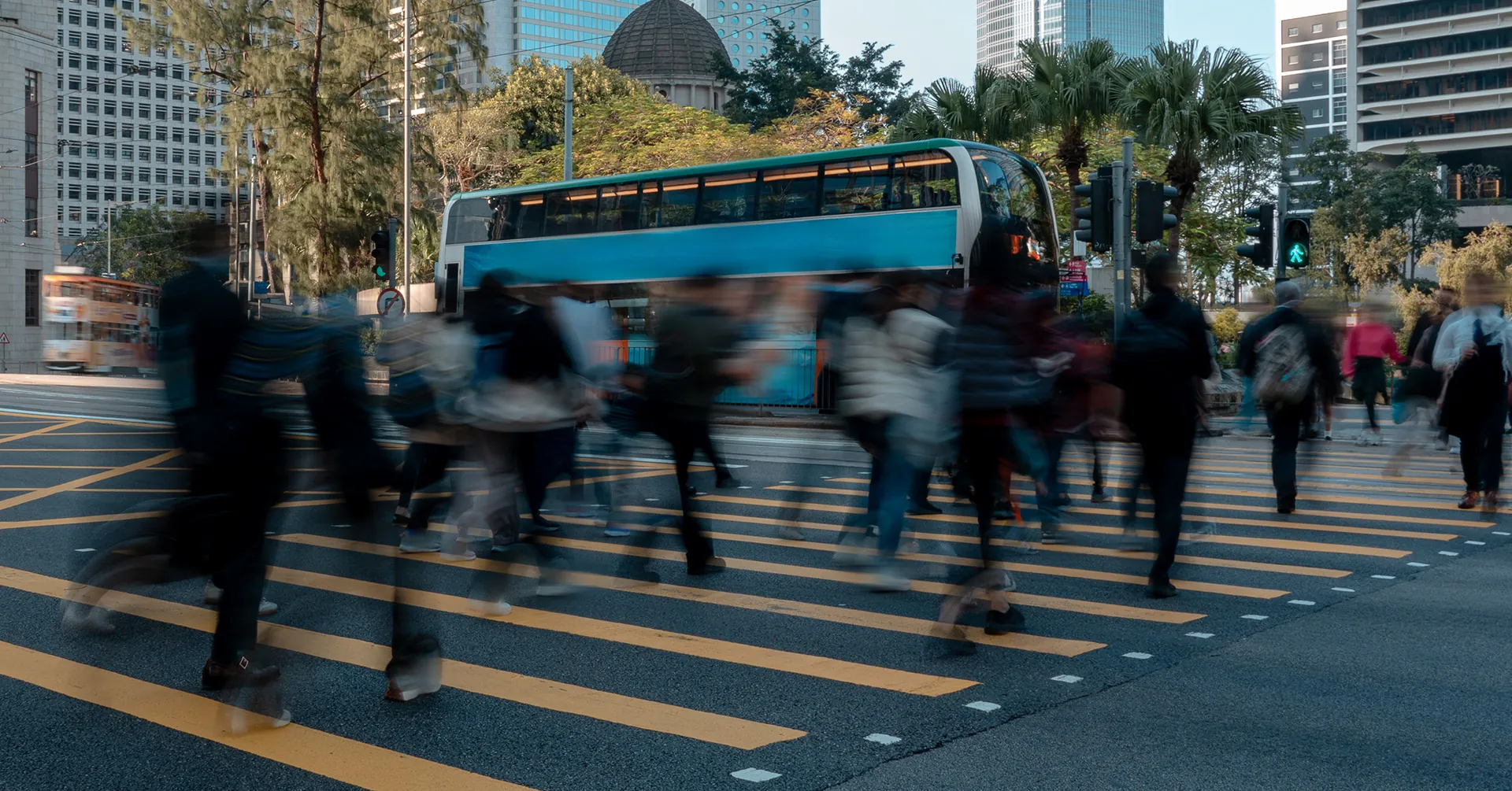
Step 2: Set safety goals
A really strong safety culture holds everyone in the organization accountable. But accountability is possible only with clear goals and expectations. Once you have evaluated the potential safety threats to your organization, you can prioritize prevention and preparation measures. Goals can help to break up some of your bigger safety initiatives and make progress feel more manageable.
These goals could take a top-down approach—for example, aiming to “reduce the number of on-the-job accidents by 50% this year”—or they could be individually driven. Some experts, such as security consultant Dave Fennell, suggest setting goals on the human level. With this approach, the goal might be to meet one-on-one with all safety leaders to better understand their needs or to improve systems such as incident reporting.
Step 3: Ensure everyone is involved and committed
Lasting cultural change does not result from simple instruction or imposition. Instead, building a strong safety culture requires leadership support and employee engagement. Whether people work in a warehouse, office, factory, field, or remote location—a coherent safety culture needs everyone to buy in. For companies with established cultures, consider implementing safety change management to help with the transition. Even for new hires, you can orient them with a culture-focused onboarding experience to engage them in safety goals alongside the company’s other leading values.
In a webinar on safety culture, Mark French, the CHRO at Dalkia Energy Solutions, shared an example of effective cultural change. Alcoa is an industrial company heavily involved in metallurgy. When former CEO Paul O’Neill joined the company in 1987, he focused on establishing safe work practices and radically reducing the number of injuries sustained by Alcoa workers.
To effect real change, O’Neill didn’t strategize only with the company’s leadership. He talked to employees at all levels and invited them to share their concerns about the company’s safety management. With workplace culture changes starting on the ground level, Alcoa was not only able to improve its safety performance but was also able to gain a deeper understanding of its manufacturing processes and optimize the business overall.
Step 4: Develop emergency response plans and safety responsibilities
During an emergency, it becomes much more difficult to make decisions on the spot. That’s why it’s crucial not to wait until a disaster strikes before developing response plans, including clear safety responsibilities, so everyone will be prepared.
Since you’ve already identified the relative likelihood and potential severity of any reasonable risk, you can now prepare for each of those incidents accordingly. Your emergency response plans must be rooted in your evaluation from step 1.
While developing these plans, it is imperative that you loop in those who currently work in those conditions. They’re usually the people who are most aware of how their job and work environment can be improved, especially when it comes to safety. At this level, you will also need to identify safety leaders who can fulfill specific responsibilities in support of your emergency response plans. These people can also act as safety culture champions even when it’s business as usual to help sustain employee engagement in regular safety practices.
Since these safety leader responsibilities might change as people shift roles or join and leave the company, it is vital that these assignments and responsibilities are recorded in your detailed planning documents—ideally with digital access—so it’s easy to update roles and to onboard new safety leaders.
It might seem impossible to predict every eventuality, but it’s definitely doable if you include your colleagues in the process.
Step 5: Develop and implement safety training programs
Once you know what safety practices look like for your business, it’s time to create a “lesson plan” so you can train everyone on the procedures planned for specific safety hazards. OSHA recommends using hands-on training to get workers up to speed on various safety practices. A safety calendar can help everyone remember when training programs, initiatives, and other activities occur.
If employees are trained only by listening to a safety lecture or watching a short video, they’re unlikely to retain the information well enough to ensure positive safety outcomes. Rather, safety training programs need to offer hands-on practice for all employees who do such work. For example, if you’re training someone on how to properly wear a safety harness, having an experienced coworker walk them through it a few times is the best way to teach safety procedures and prevent unsafe behaviors.
On an episode of the Employee Safety Podcast, safety expert Shawn Rafferty describes how, in an emergency, people do what comes naturally to them. If they don’t have the muscle memory to do something, they probably won’t be able to when they’re in trouble. Hence, we have even more reason to equip employees with effective training so safety rules and habits do come naturally to them in stressful situations.
The kind and amount of training that an employee receives should be determined by their role. Heavy machinery operators have different safety concerns than their counterparts who sit behind a desk in a private office. A successful safety culture addresses individual and group needs in preparation for and during an emergency. Regardless of the role, safety training should be systematized, easy to adopt, and derived from the experiences of workers.
Step 6: Establish methods of reporting and communication
If one of your employees is going about their daily business and they encounter an emergency situation that they have to deal with, it’s likely that they will get tunnel vision and focus solely on the problem right in front of them. Not only is this a detriment to situational awareness, but it often has a negative impact on safety as well. But there are important lessons to take away from these situations. If employees aren’t empowered to properly report safety incidents to an emergency manager or log the event in a computer system, then both incident response and the entire culture of safety will suffer.
Effective safety culture involves broader processes around any emergency incident. Once the immediate danger or issue has been mitigated, that incident must be logged and treated as a lesson to inform and improve safety policies. Ensure that you record all safety incidents, even so-called “near misses” that didn’t result in a problem. And build proactive communication pathways to keep employees informed of updated procedures, to avoid misinformation, and to keep everyone focused on the task at hand.
Even when there isn’t an emergency taking place, communication still has an important role to play in building a strong safety culture. Non-emergent communications can increase the level of transparency, accountability, and openness within your business—all of which means that the company feels more in sync when it comes to safety.
To that end, communication technology can be extremely helpful. Emergency communication systems, such as AlertMedia’s, allow you to quickly, accurately, and reliably reach your people across multiple messaging channels. Along with complete, up-to-date record-keeping of employee roles, contact info, work schedules, and locations, you have the ingredients for seamless alignment even during stressful times. The right communication platform also allows you to upload the necessary info to a secure, yet easy-to-access system. You can even include information from suppliers, customers, and others in your community with whom you would like to share safety information.
A strong safety culture is possible only when it is interwoven with the entire human fabric of the company, and you can’t do that if you don’t know who’s who and how to get in contact with them.
Step 7: Exchange feedback and monitor your safety culture
If you’ve followed the previous steps, your entire organization will be doing a lot to bolster safety on a daily basis. However, it’s impossible to completely eliminate workplace injuries and other dangers that might come with a job. That’s why you need a strong safety culture that normalizes feedback for your employees and from your employees.
When giving feedback, don’t be a “safety cop.” Our job as safety professionals isn’t simply to call out safety errors but rather to fix underlying gaps in the organizational culture of safety. Handing out demerits for small lapses in safety rules can lead to bigger lapses in people’s trust, and employees may be less likely to give you honest feedback or even to report safety violations in the first place. OSHA also promotes positive feedback as more effective than negative feedback.
Building a positive safety culture means actively listening to workers and hearing their observations and concerns. After all, they’re the boots on the ground, so to speak, of your safety efforts. If they’re running into roadblocks, encourage employees to escalate those safety issues and engage leadership support to follow up with real improvements.
Step 8: Commit to continuous improvement
Mark French of Dalkia stresses that even if you reach the goal of zero safety incidents, you can’t let up. No matter how good your safety performance has been or how smoothly things are going, there’s no guarantee that it will remain that way forever.
Aim for iterative improvement. The strength of your safety culture depends on the organization’s ability to adapt to internal and external changes, to learn from incidents, and to keep safety top of mind. Regularly reassess the risks to your people and your business, and reevaluate your safety goals. Analyze the effectiveness of your communication tools and strategies as your business and its vulnerabilities evolve. If you’re also keeping records and collaborating with your team, your safety outcomes will continue to improve. Building a safety culture is an ongoing commitment.
Start Now With Real Cultural Change
Anyone who’s spent time working to improve the well-being of their coworkers knows that safety isn’t just a thing that someone does; it’s not a line item to be checked off the to-do list and forgotten about. The best way to make sure everyone at your company stays safe is to focus on building an omnipresent culture of safety.
When a commitment to safety is built into the very fabric of the company, better safety outcomes are all but assured. Try implementing these steps at your own organization and see how you can create a safety culture of your own.